Condition Monitoring of Bearings
Ultrasound Monitoring in Bearings Analysis
Our Product: We render our services in ‘Ultrasound Monitoring of Bearings’.
Ultrasound Bearing Inspection Ultrasonic inspection and monitoring of bearings is by far the most reliable method for detecting incipient bearing failure. The ultrasonic warning appears prior to a rise in temperature or an increase in low frequency vibration levels. Ultrasonic inspection of bearings is useful in recognizing:
Our Product: We render our services in ‘Ultrasound Monitoring of Bearings’.
Ultrasound Bearing Inspection Ultrasonic inspection and monitoring of bearings is by far the most reliable method for detecting incipient bearing failure. The ultrasonic warning appears prior to a rise in temperature or an increase in low frequency vibration levels. Ultrasonic inspection of bearings is useful in recognizing:
-
The beginning of fatigue failure: In ball bearings, as the metal in the raceway, roller or ball bearing begins to fatigue; a subtle deformation begins to occur. This deforming of the metal will produce irregular surfaces, which will cause an increase in the emission of ultrasonic sound waves.
A change in amplitude from the original reading is an indication of incipient bearing failure. When an ultrasonic reading exceeds any previous reading by 12 dB, it can be assumed that the bearing has entered the beginning of the failure mode
-
Brinelling of bearing surfaces: Brinelling of bearing surfaces will produce a similar increase in amplitude due to the flattening process as the balls get out of round. These flat spots also produce a repetitive ringing that is detected as an increase in amplitude of monitored frequencies.
-
Flooding of or lack of lubricant: It is important to consider two elements of potential failure. One is lack of lubrication while the other is over-lubrication.
As the lubricant film reduces, the sound level will increase. A rise of about 8 dB over baseline accompanied by a uniform rushing sound will indicate lack of lubrication.
Procedure:
Procedure:
-
You have to identify the bearings under monitoring & List it.
-
Trust us the periodic ‘Ultrasound Monitoring of Bearings’.
-
The frequency of monitoring has to be scheduled by you, fortnightly / monthly / quarterly.
-
After every inspection, we will submit report for every bearing under inspection in which we will give peak and RMS values of the noise level. Crest factor of every bearing will be recorded in the report.
-
The condition of bearing then will be studied, confirmed, and recorded in the report.
-
After three consecutive inspections, report on trend analysis will be done for every bearing under inspection and will be studied.
-
Our conclusions, recommendations, and suggestions will be given with every report.
![]() |
![]() |
Various stages of bearing failures have been identified:
-
8 dB above the basic / average value indicates a lack of lubrication;
-
12 dB above the basic / average value indicates the start of bearing damage;
-
16 dB above the basic / average value indicates a very advanced stage of visible bearing damage;
-
35 to 50 dB an increase of the basic / average value which indicates heavy bearing damage.
Rolling element bearings are key components in rotating machines, and bearing failure is a major cause of costly breakdowns. Bearing failures can be catastrophic and result in significant downtime and maintenance costs, especially for those applications with limited accessibility
Once established, ultrasound can be used as the “first line of defense”. Ultrasound may be the first signal that bearing gives and alerts well before in time.
A defect symptom may be as simple as an increase in friction from poor lubrication. Another symptom may be the rubbing and skidding of rolling elements against the bearing raceway, or impacting due to mechanical flaws or contaminated lubricant. A defect condition could be misalignment, imbalance, or worn shaft couplings. Other causes of bearing failure include improper installation, corrosive atmospheres, particle contamination, faulty alignment, and use of the wrong lubricant.
As a front line defense against symptoms of failure, ultrasound raises alarm flags very early on. It answers the most simple and fundamental question: “Is my machine okay?”
By using ultrasound to filter the good from the bad, they afford themselves more time to perform deeper (Vibration) analysis on only the machines designated as “not okay” by ultrasound. Serving once again as a symbiotic companion to vibration analysis,
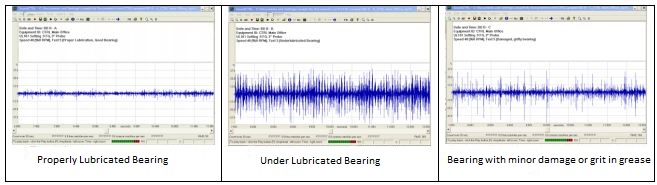
ultrasound performs exceptionally well in assessing defects on slow rotating assets, an area where vibration analysis can struggle.
As ball or Roller bearings rotate the friction and impacts between the parts generate ultrasound. Normally operating bearings produce a steady level of ultrasound. If the bearings are under lubricated this becomes much louder and harsher. Conversely over lubricated (this can give rise to overheating and rapid degradation of the lubricant) bearings make very little sound.
As ball or Roller bearings rotate the friction and impacts between the parts generate ultrasound. Normally operating bearings produce a steady level of ultrasound. If the bearings are under lubricated this becomes much louder and harsher. Conversely over lubricated (this can give rise to overheating and rapid degradation of the lubricant) bearings make very little sound.